Das Spritzgießverfahren bietet die einfachste Möglichkeit, die zu verbindenden Formteile schweißgerecht herzustellen. Bei der Konstruktion der Formteile der Auslegung der Sonotrode und des Aufnahmewerkzeuges sowie beim Schweißen sind einige wichtige Faktoren zu beachten, Beispiele sind in den nachstehend aufgeführten Kapiteln beschrieben.
Das unterschiedliche Schweißverhalten der thermoplastischen Kunststoffe ist bei der Werkstoffauswahl zu berücksichtigen, Die zu verbindenden Formteile müssen so konstruiert sein, dass die zum Schweißen notwendige Plastifizierung reproduzierbar in der Fügefläche eintritt.
Zum Erzielen hochwertiger Verbindungen sind bereits in der Planungsphase die nötigen Voraussetzungen zu schaffen. Je nach Anforderung an die Schweißverbindung ist die Konstruktion u.a. auf folgende Forderungen auszurichten:
- Belastbarkeit der Schweißnaht
- Dichtigkeit gegenüber Flüssigkeiten und Gasen
- optisch ansprechendes Aussehen
- Vermeiden von Schmelzeaustrieb und Kunststoffpartikeln im Innern der Formteile.
Die erzielbare Qualität der Schweißverbindung wird neben den Schweißparametern, noch von folgenden Faktoren beeinflusst:
- Art des Werkstoffes
- Konstruktion des Formteils
- Lage und Ausbildung der Fügeflächen
- Anordnung der Energierichtungsgeber
- Positionierung und Passungsspiel zwischen Ober- und Unterteil
- Ankopplung der Sonotrode
- Freier Einsinkweg
- Auflage im Aufnahmewerkzeug.
Konstruktion der Formteile Die Formteile sind formsteif auszuführen. Es sind genügend dicke Wandungen vorzusehen, Bei zu dünnwandigen Formteilen besteht die Gefahr der Beschädigung.
Ausrunden von Ecken und Kanten
Alle Ecken und Kanten sind an den Formteilen genügend auszurunden. Vorgeschlagen werden Mindestradien von 0,2 bis 0,15 mm. Dies ist, besonders bei harten Kunststoffen wichtig. Zu scharfe Übergänge können beim Ultraschall-Schweißen zu Rissen führen.
Lage der Fügefläche und die Entfernung zur Sonotode
Die Lage der Fügefläche sollte möglichst senkrecht zur Sonotrodenachse und parallel zur Sonotrodenstirnfläche angeordnet seine Auch sollte die Fügefläche in einer Ebene liegen. Wo dies nicht realisierbar ist, empfiehlt sich ein Kontakt mit den Ultraschall-Geräte- bzw. Rohstoffherstellern. Die Entfernung Sonotrodenstirnfläche/FügefIäche sollte gering sein.
Größe und Ausbildung der Fügefläche
Die Fügeflächengeometrie ist auf die Anforderungen an die Schweißnaht abzustimmen. Entscheidende Faktoren sind:
- Art des Werkstoffes
- Konstruktion des Formteils.
Zum Erzielen kurzer Schweißzyklen und Vermeiden von Beschädigungen sind Energierichtungsgeber (Energiekonzentratoren) vorzusehen. Man unterscheidet kegel-, noppen- und dachförmige Energierichtungsgeber sowie die als Energierichtungsgeber wirkenden Kantenberührungen bei Quetschnähten.
Energierichtungsgeber (ERG)
Der Energierichtungsgeber hat die Aufgabe, die Plastifizierung der Fügefläche durch Energiekonzentration schnell einzuleiten. Die Form und Größe der ERG ist in bestimmten Grenzen frei wählbar. Je nach Art des Kunststoffes, der Konstruktion des Formteils und der Anforderung an die Schweißverbindung sind folgende Grundformen, zu unterscheiden:
- Kegel- bzw. noppenförmige Energierichtungsgeber
- Dachförmige Energierichtungsgeber
- Kantenberührungen bei Einfach- und Doppelquetschnähten.

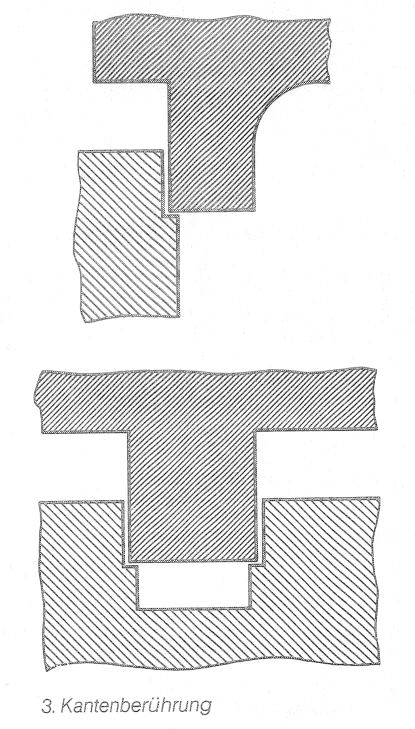
In der Regel ist es für das Schweißergebnis unerheblich, auf welcher Formteilhälfte die ERG vorgesehen werden. In Sonderfällen (wie bei unterschiedlichen Kunststoffkombinationen) ist die günstigste Lage durch Versuche zu klären. Bei Formteilen mit unterschiedlicher Steifigkeit sind die ERG im weicheren Formteil anzuordnen.
Zentrierung der Formteile
Formoberteil und Unterteil sind so zu zentrieren, dass sie beim Schweißen ihre Position beibehalten. Die Zentrierhöhe sollte nicht unter 1 mm liegen. In der Regel ist eine Zentrierung über das Formteil anzustreben.
Das Passungsspiel zwischen Ober- und Unterteil sollte gering sein, jedoch mindestens 0,05 mm betragen. Dieses Spiel muss auch bei schrägen und konisch zulaufenden Wandungen bis zur endgültigen Einsinktiefe vorhanden sein. Bei der Kombination von Formteilen aus unterschiedlichen Kunststofftypen (z. B. verstärkt/unverstärkt) sind deren unterschiedliche Schwundmaße zu beachten.
Folgende Zentrierungsmöglichkeiten, werden gewählt:
- durch die Geometrie der Fügeflächen
- durch Zapfen und Bohrung
- durch das Aufnahmewerkzeug
- mittels Zentrierung durch Sonotrode und Aufnahmewerkzeug. (Nur anwendbar bei besonders hoher Maßgenauigkeit der Formteile. Diese Zentriermöglichkeit wird nur in Sonderfällen genutzt.)
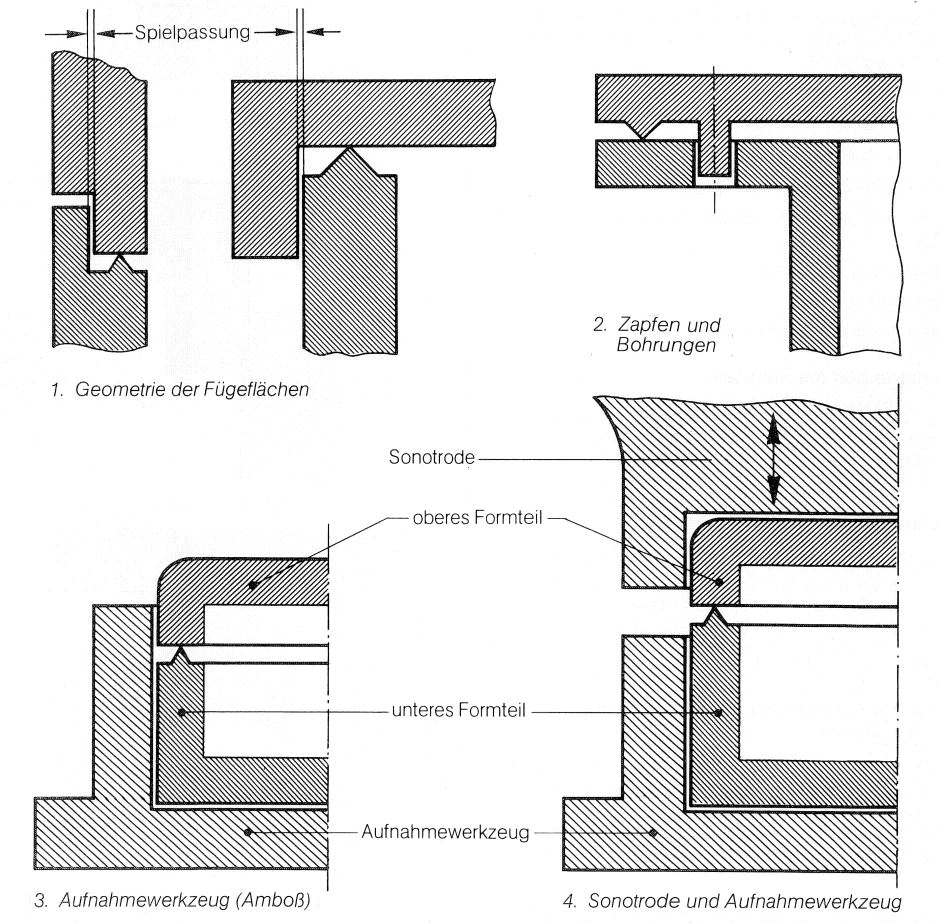
Freier Einsinkweg des Oberteils
Das Oberteil muß beim Ultraschall-Schweißen frei einsinken können. Kanten, Rippen oder Stege dürfen das Oberteil bei der Einsinkbewegung nicht abfangen.
Mitschwingen von Rippen, Laschen, Bolzen und anderen Funktionselementen
Freistehende Rippen, Laschen, Bolzen sowie Einlegeteile können bei der Schallübertragung beschädigt werden. Durch genügend große Radien an Ecken, Kanten und Übergängen, kurze Schweißzeiten oder auch mit schwingungsdämpfenden Unterlagen ist Abhilfe möglich.
Lösen von Partikeln beim Schweißen
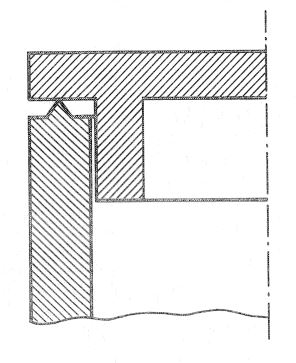
Beim Schweißen können sich Partikel von der Schweißnaht oder deren Umgebung lösen und ins Innere der Formteile gelangen, Dies lässt sich weitgehend durch Verdecken der Schweißnaht vermeiden.
Auflage im Aufnahmewerkzeug
Das untere Formteil ist im Aufnahmewerkzeug genügend abzustützen und für den Schweißvorgang zu zentrieren. Bei dünnwandigen Formteilen und besonders bei Quetschnähten ist ein Abstützen der Seitenwände bis nahe zur Fügezone empfehlenswert.
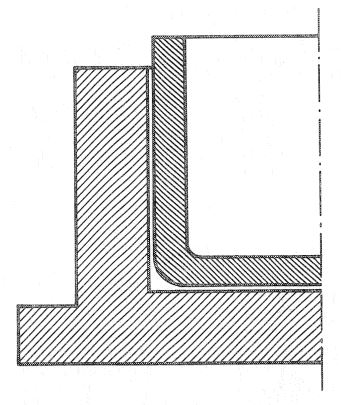
Ankopplungsfläche der Sonotrode
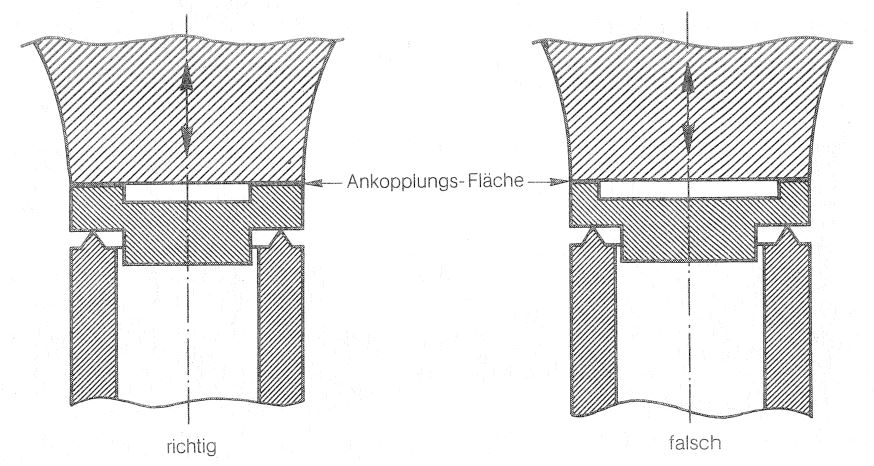
Für die Ankopplungsfläche der Sonotrode ist möglichst eine ebene, dem Formteil angepasste und ausreichend groß bemessene Fläche vorzusehen. Bei zu klein bemessenen Flächen wird die Einleitung des Ultraschalls vermindert. Beschädigungen der Ankopplungsfläche sind die Folge.
Ein gleichmäßiges Berühren der Sonotrode auf der Formteiloberfläche lässt sich z.B. durch Tuschieren oder mit Kohlepapier, dem ein weißer dünner Papierbogen beigelegt ist, nachweisen. Die Ankopplung der Sonotrode auf hochglänzenden oder strukturierten Oberflächen kann zu Markierungen führen. Solche Abdrücke lassen sich durch eine Folienzwischenlage, z. B. einer PE-Folie, mindern.
Fügeflächengeometrie
Wenn keine Erfahrungen bei der Dimensionierung der Energierichtungsgeber vorliegen, ist es aus Gründen der leichteren Nacharbeit von Spritzgießwerkzeugen zweckmäßig, mit geringeren Höhen der Energierichtungsgeber (ERG) zu beginnen.
Fügeflächenausbildung mit kegel- und noppenförmigen Energierichtungsgebern
Solche ERG lassen sich beim Verbinden von Formteilen und flächigen Teilen anwenden. Das Bild 15 ein Formunterteil mit kegelförmigen Energierichtungsgebern. Sie eignen sich nicht für Dichtschweißungen. Der Winkel a beträgt ca. 60 bis 90° . Die Höhe der ERG liegt zwischen 0,2 und 1 mm. Bei den teilkristallinen Kunststoffen sind die ERG in der Regel höher auszubilden als bei den amorphen Kunststoffen.
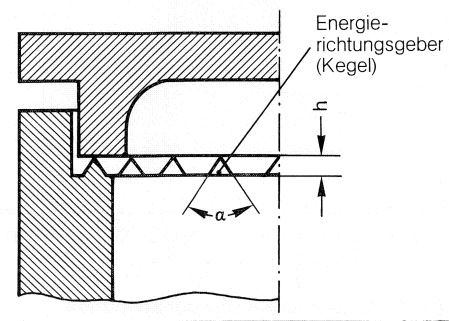
Fügeflächenausbildung mit dachförmigen Energierichtungsgebern
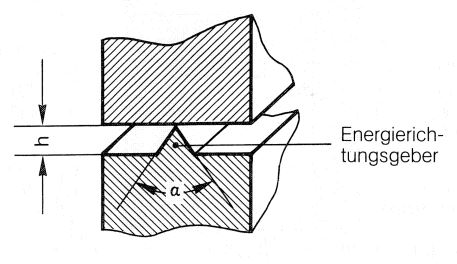
Schweißnahtgeometrien mit dachförmigen ERG sind nahezu bei allen Formteilabmessungen anwendbar. Der ERG sollte einen Winkel zwischen 60 0 und 90 0 haben. Die Höhe h kann, je nach Anforderung an die Schweißverbindung, zwischen 0,2 und 1 mm, in Sonderfällen bis 2 mm, gewählt werden.
Ein symmetrisch angeordneter ERG ist einem unsymmetrischen vorzuziehen. Er sollte die gegenüberliegende Fügefläche möglichst mittig treffen. In Sonderfällen können anstelle eines großen auch mehrere kleine ERG gewählt werden. Sie lassen sich versetzt, wie auch unterschiedlich hoch anordnen. Nachstehend einige bewährte Fügeflächenformen mit dachförmigen ERG. In bestimmten Grenzen können sich deren Proportionen noch ändern. Ebenso sind Sonderformen möglich.
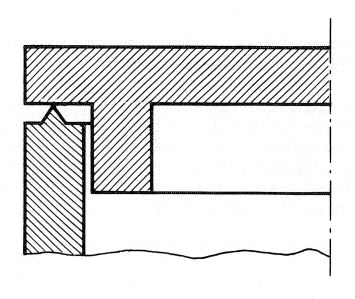
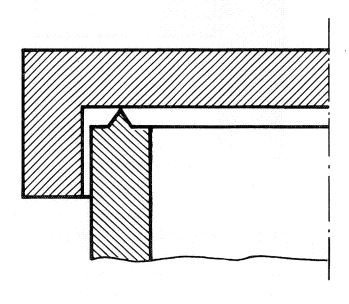
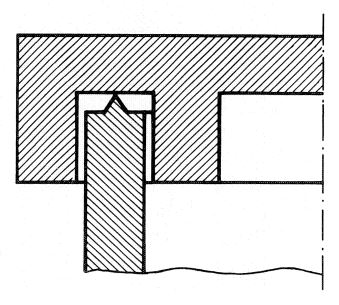
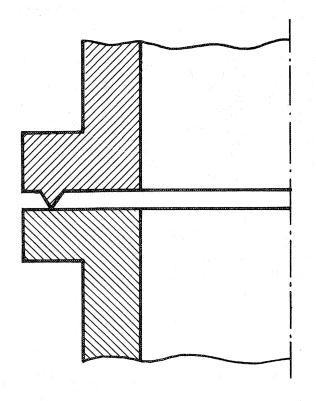
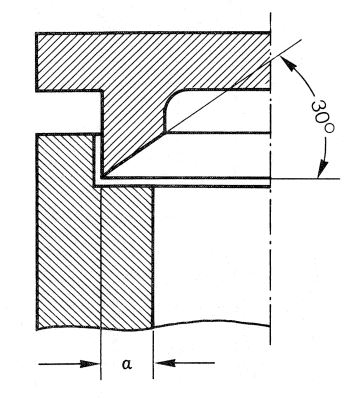
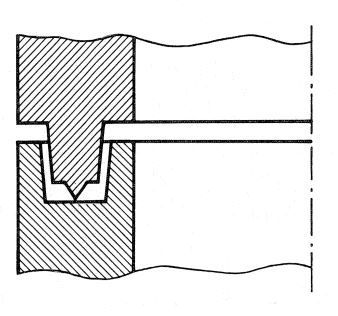
Fügeflächenausbildung mit Quetschnähten
Quetschnähte (Stufennähte) werden bevorzugt für Dichtschweißungen und bei der Verwendung von teilkristallinen Kunststoffen gewählt. Die Formteile sollten eng toleriert und das Passungsspiel gering sein. Die Seitenwände der Unterteile sind bis zur Höhe der Schweißnaht abzustützen.

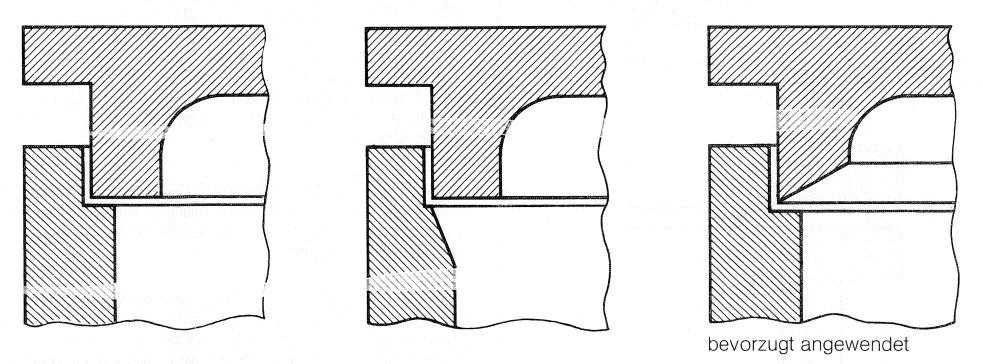
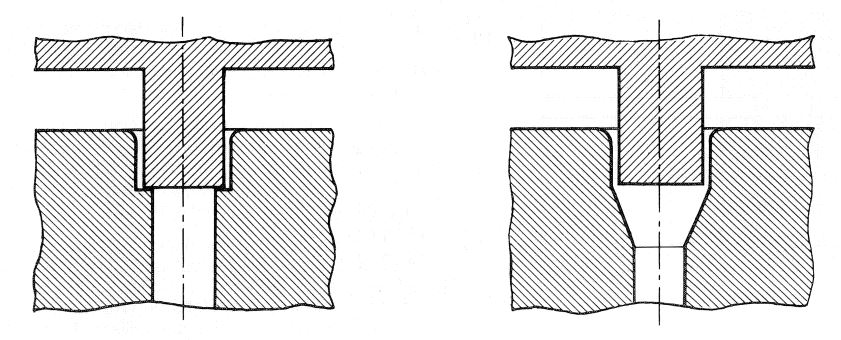